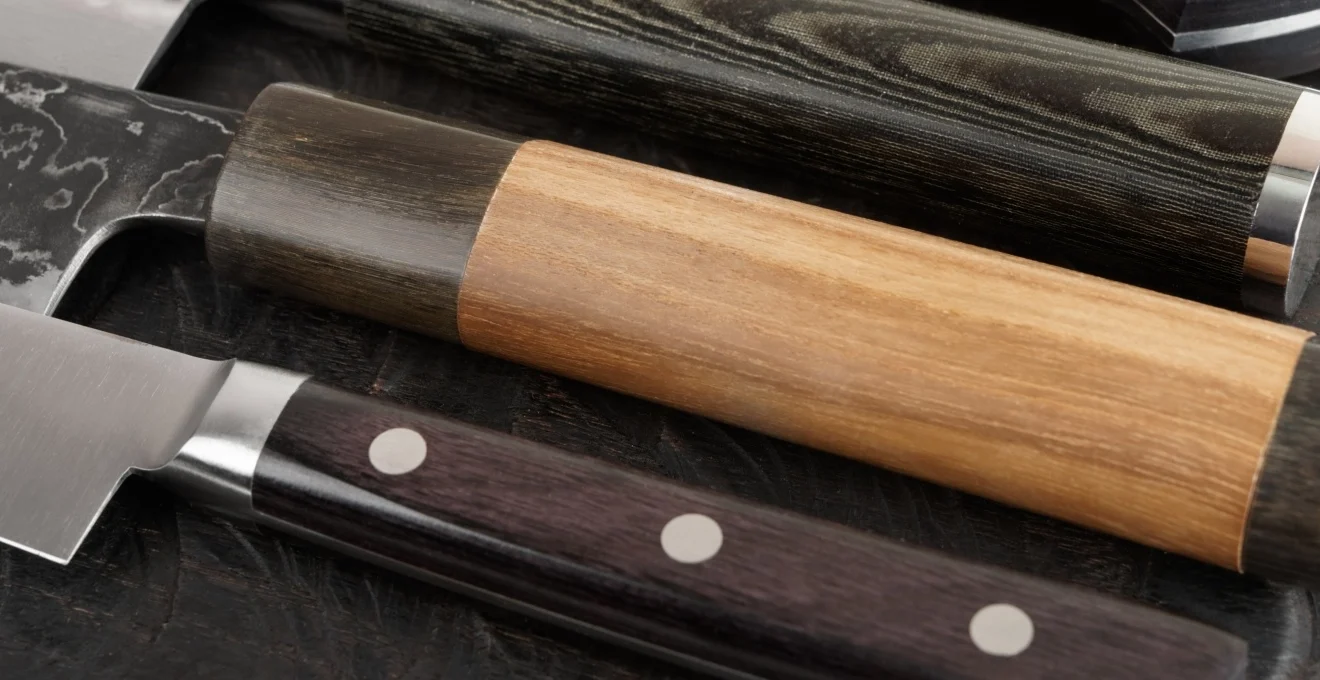
Knife enthusiasts and craftsmen alike have long appreciated the beauty and functionality of wooden handles. However, the advent of stabilized and colored wood has revolutionized the art of knife making, offering unparalleled durability, aesthetic appeal, and customization options. This innovative process combines the natural charm of wood with cutting-edge technology, resulting in handles that are not only visually striking but also incredibly resilient.
Chemical processes in wood stabilization for knife handles
The transformation of ordinary wood into a superior material for knife handles involves a complex chemical process. At its core, wood stabilization aims to fill the porous structure of the wood with a hardening resin, effectively "petrifying" it while maintaining its natural appearance. This process begins with thoroughly drying the wood to remove all moisture, creating space within the cellular structure for the resin to penetrate.
Once dried, the wood is placed in a vacuum chamber where air is removed from its pores. A liquid resin, typically a thermosetting polymer, is then introduced. As the vacuum is released, the resin is forced into the wood's cellular structure, filling voids and bonding with the wood fibers at a molecular level. The final step involves curing the resin, usually through heat treatment, which solidifies it and completes the stabilization process.
The choice of resin is crucial, as it affects the final properties of the stabilized wood. Acrylics are commonly used due to their clarity and ability to carry pigments, while epoxy resins offer superior hardness and chemical resistance. Some craftsmen even experiment with hybrid resins to achieve specific characteristics in their knife handles.
Wood stabilization is not just a treatment; it's a complete metamorphosis that enhances the wood's natural beauty while overcoming its inherent weaknesses.
The chemical bonding between the wood fibers and the cured resin creates a composite material that is significantly more stable and resistant to environmental factors than untreated wood. This synergy results in a handle material that maintains the warmth and tactile appeal of wood while offering the durability and consistency of synthetic materials.
Coloration techniques for stabilized wood
The coloration of stabilized wood opens up a world of creative possibilities for knife makers and collectors. Unlike surface treatments, the colors in stabilized wood penetrate deep into the material, ensuring long-lasting vibrancy and unique patterns that can't be achieved with traditional wood finishing techniques. Let's explore some of the most effective methods used to add color to stabilized wood.
Vacuum-pressure dye infusion methods
Vacuum-pressure dye infusion is a sophisticated technique that allows for deep, uniform coloration of stabilized wood. This process involves dissolving dyes in the stabilizing resin before it's introduced to the wood. When the resin is forced into the wood under pressure, it carries the dye along with it, resulting in color that permeates the entire piece.
The key advantage of this method is the depth and consistency of color it achieves. By varying the concentration of dyes and the pressure applied, craftsmen can control the intensity of the color and create subtle gradients within the wood. This technique is particularly effective with lighter woods like maple or birch, where the natural grain can still be visible through the added color.
You can find a wide variety of pre-colored and stabilized wood blanks for knife handles at mercorne.fr, offering a range of options for both amateur and professional knife makers.
Double-dye processes for complex color patterns
For those seeking more intricate and unique color patterns, the double-dye process offers exciting possibilities. This technique involves applying two different colors to the wood in stages, often with a partial sanding step in between. The result is a layered effect that can create stunning visual depth and complexity in the finished handle.
The process typically begins with a lighter base color that is allowed to partially penetrate the wood. After curing, the surface is lightly sanded to reveal some of the natural wood grain. A second, contrasting color is then applied, which settles into the exposed grain and any remaining porous areas. This creates a dynamic interplay between the two colors and the wood's natural patterns.
Double-dyeing requires skill and patience, as the timing and pressure of each dye application can significantly affect the final outcome. However, when executed well, it can produce truly one-of-a-kind knife handles that are as much works of art as they are functional tools.
Uv-resistant pigments for outdoor knife applications
For knives that will see extensive outdoor use, UV resistance is a critical consideration in the coloration process. Standard dyes can fade or change color when exposed to sunlight over time, compromising both the aesthetics and value of the knife. To combat this, many craftsmen turn to UV-resistant pigments when coloring stabilized wood for outdoor knife handles.
These specialized pigments are designed to maintain their color integrity even under prolonged sun exposure. They work by either reflecting or absorbing UV radiation without degrading, ensuring that the vibrant colors of the knife handle remain true for years to come. While slightly more expensive, the use of UV-resistant pigments is a worthwhile investment for any knife intended for outdoor enthusiasts or professionals working in sun-exposed environments.
Incorporating these pigments often requires adjusting the stabilization and dyeing process to ensure proper dispersion and bonding within the wood structure. The result is a knife handle that not only looks impressive but also maintains its appearance in challenging outdoor conditions.
Material properties of stabilized wood in knife making
The transformation of wood through stabilization significantly alters its physical properties, making it an ideal material for knife handles. Understanding these enhanced characteristics is crucial for both knife makers and enthusiasts who want to appreciate the full value of stabilized wood in their tools.
Density and hardness improvements through resin impregnation
One of the most notable changes in stabilized wood is the dramatic increase in density and hardness. The impregnation of resin into the wood's cellular structure fills voids and reinforces the natural fibers, resulting in a material that is significantly denser than its untreated counterpart. This increased density translates to improved hardness, often measured using the Janka hardness test.
For example, a piece of stabilized maple can have a Janka hardness rating up to 50% higher than untreated maple. This enhanced hardness provides several benefits for knife handles:
- Increased resistance to dents and scratches
- Improved durability in high-stress areas like the bolster
- Better retention of fine details and textures during shaping and finishing
- Enhanced overall lifespan of the knife handle
The improved density also contributes to a more substantial feel in the hand, which many users appreciate for its perceived quality and balance.
Moisture resistance and dimensional stability
Perhaps the most significant advantage of stabilized wood for knife handles is its exceptional moisture resistance and dimensional stability. Natural wood is hygroscopic, meaning it absorbs and releases moisture in response to environmental conditions. This can lead to swelling, shrinking, and warping—all undesirable traits in a knife handle.
Stabilized wood, however, has its porous structure filled with cured resin, effectively sealing it against moisture intrusion. This results in a material that maintains its shape and size regardless of humidity levels or exposure to water. The benefits of this stability include:
- Consistent fit and finish over time, even in varying climates
- Reduced risk of cracking or splitting due to moisture-related stress
- Improved resistance to rot and fungal growth
- Easier maintenance and cleaning without fear of water damage
This stability is particularly valuable for outdoor and hunting knives, which may be exposed to harsh and varying environmental conditions.
Impact on knife balance and ergonomics
The altered physical properties of stabilized wood also have a significant impact on the overall balance and ergonomics of a knife. The increased density of stabilized wood allows for more precise weight distribution in the handle, which can be crucial for achieving optimal balance in the finished knife.
Knife makers can take advantage of this by carefully selecting and positioning stabilized wood components to achieve the desired balance point. This level of control was previously difficult to achieve with natural wood due to its variability in density and moisture content.
Additionally, the dimensional stability of stabilized wood ensures that the carefully crafted ergonomics of a knife handle remain consistent over time. Features like finger grooves, palm swells, and texture patterns maintain their shape and effectiveness, providing a reliable and comfortable grip year after year.
Popular wood species for stabilized knife handles
While virtually any wood species can be stabilized, certain types have become favorites among knife makers and enthusiasts due to their unique characteristics and aesthetic appeal when treated. Let's explore some of the most popular wood species used for stabilized knife handles.
Burl woods: maple, oak and redwood
Burl woods are prized for their intricate, swirling grain patterns that create visually stunning knife handles. When stabilized, these patterns become even more pronounced, often taking on a three-dimensional quality that catches the eye and adds depth to the handle.
Maple burl is particularly popular due to its availability and the way it takes on dyes. Stabilized maple burl can range from subtle, natural tones to vibrant, almost psychedelic patterns when dyed. Its fine grain structure allows for smooth finishing and comfortable grip.
Oak burl, while less common, offers a more pronounced grain pattern with larger swirls and eyes. Stabilized oak burl handles are often left in their natural color to showcase the wood's inherent beauty and complexity.
Redwood burl is sought after for its rich, warm tones and unique patterns. When stabilized, redwood burl can achieve an almost glass-like finish while maintaining the depth and character of its natural grain.
Exotic hardwoods: bocote, cocobolo and ebony
Exotic hardwoods bring their own unique colors and grain patterns to knife handles, which are further enhanced through stabilization. These woods are often chosen for high-end custom knives and collectors' pieces.
Bocote is known for its striking contrast between light and dark streaks. When stabilized, these contrasts become even more pronounced, creating a dynamic and eye-catching handle. The wood's natural oils can sometimes interfere with the stabilization process, requiring careful preparation.
Cocobolo is prized for its rich, reddish-brown color and fine grain. Stabilization helps to preserve the wood's vibrant color, which can otherwise darken significantly over time. The stabilization process also mitigates the allergenic properties of cocobolo dust, making it safer to work with.
Ebony is valued for its deep black color and extremely fine grain. While naturally very dense, stabilization can further enhance its durability and reduce its tendency to crack. Stabilized ebony provides an elegant, classic look that pairs well with polished metal fittings.
Spalted woods: beech and tamarind
Spalted woods offer some of the most unique and artistic patterns in knife handles. Spalting is caused by fungal growth in wood, creating intricate black lines and color variations. However, this process can weaken the wood, making stabilization particularly beneficial.
Spalted beech is highly sought after for its dramatic black lines contrasting against a light background. Stabilization not only preserves these patterns but also restores the strength lost during the spalting process. The result is a handle material that combines natural art with practical durability.
Spalted tamarind is less common but offers equally stunning results. Its patterns tend to be more varied, with zones of different colors and textures. When stabilized, spalted tamarind can produce handles with an almost abstract, painterly quality.
The stabilization process is particularly crucial for spalted woods, as it halts the decay process and ensures that the beautiful patterns are preserved indefinitely. It also allows knife makers to work with wood that would otherwise be too soft or fragile for practical use.
Advanced finishing techniques for stabilized wood handles
The finishing process for stabilized wood handles is where craftsmanship truly shines, bringing out the full potential of this remarkable material. Advanced techniques can elevate a well-made handle into a work of art, enhancing both its aesthetic appeal and functional properties.
High-grit sanding sequences for mirror finishes
Achieving a mirror finish on stabilized wood requires patience and precision. The process typically involves a carefully planned sequence of progressively finer grit sandpapers. Many craftsmen start with grits as low as 220 and work their way up to ultra-fine grits of 2000 or even higher.
The key to success lies in not skipping grits and ensuring that all scratches from the previous grit are completely removed before moving to the next. This meticulous process can involve 10 or more steps, but the results are worth the effort. A properly executed high-grit sanding sequence can produce a surface so smooth and reflective that it rivals polished metal.
For optimal results, consider the following tips:
- Use a firm backing pad to ensure even pressure across the surface
- Alternate sanding direction between grits to easily identify missed spots
- Clean the surface thoroughly between grits to prevent cross-contamination
- Use a magnifying glass to inspect the surface for consistency
Buffing compounds and their applications
After high-grit sanding, buffing compounds can take the finish to the next level, creating a truly lustrous surface. Different compounds are used in sequence, similar to the sanding process, to achieve the desired result.
Typically, the buffing process starts with a coarse compound to remove any remaining fine scratches from sanding. This is followed by medium and fine compounds, each further refining the surface. The final step often involves a specialized polishing compound designed for wood, which can impart an incredible depth and clarity to the finish.
When working with buffing compounds on stabilized wood, keep these points in mind:
- Use separate buffing wheels for each compound to prevent cross-contamination
- Control the speed and pressure to avoid generating excessive heat
- Pay special attention to edges and corners, which can easily be over-buffed
- Consider the final look you're aiming for – some prefer a satin finish over high gloss
Hybrid Epoxy-Wood finishes for enhanced durability
For knife handles that will see heavy use or exposure to harsh conditions, a hybrid epoxy-wood finish can provide additional protection and visual appeal. This technique involves applying a thin layer of clear epoxy over the stabilized wood, creating a durable, waterproof surface that enhances the wood's natural beauty.
The process typically involves the following steps:
- Prepare the stabilized wood surface with fine-grit sanding
- Clean thoroughly to remove all dust and oils
- Mix a high-quality, clear epoxy according to manufacturer instructions
- Apply the epoxy in thin, even coats, allowing each to cure fully
- Sand lightly between coats for better adhesion
- Finish with a final coat and polish to the desired sheen
Integration of stabilized wood with other handle materials
The versatility of stabilized wood opens up exciting possibilities for combining it with other materials to create unique and functional knife handles. These hybrid designs can offer the best of both worlds, marrying the warmth and beauty of wood with the durability and performance of other materials.
One popular combination is the use of stabilized wood with metal components. Stainless steel or titanium bolsters and pins can provide structural reinforcement while creating an attractive contrast with the wood. Some knife makers even incorporate thin layers of metal between sections of stabilized wood, creating a striking laminated effect.
Another intriguing pairing is stabilized wood with synthetic materials like G10 or carbon fiber. These combinations can result in handles that offer enhanced grip in wet conditions while maintaining the aesthetic appeal of wood. For example, a handle might feature panels of stabilized burl wood inlaid into a G10 frame, providing both beauty and functionality.
Some craftsmen are pushing the boundaries even further by combining stabilized wood with natural materials like antler or bone. These organic pairings can create truly unique handles that tell a story and connect the user with nature.